Barely a scratch after months among the rocks in the shoreline
To give you a sense of the robustness and quality of the system's design, let us start with a story from one of our clients.
It was January when the fish farmer Egil Kristoffersen & Sønner lost their Blueye Pioneer ROV during an operation in the North of Norway. The tether on their ROV got caught up in the boat's propeller and the ROV lost ashore. It was windy and snowy, making searching for the lost drone hard. After reaching out for help on Facebook, it was finally found a couple of months after lying among the rocks on the shoreline.
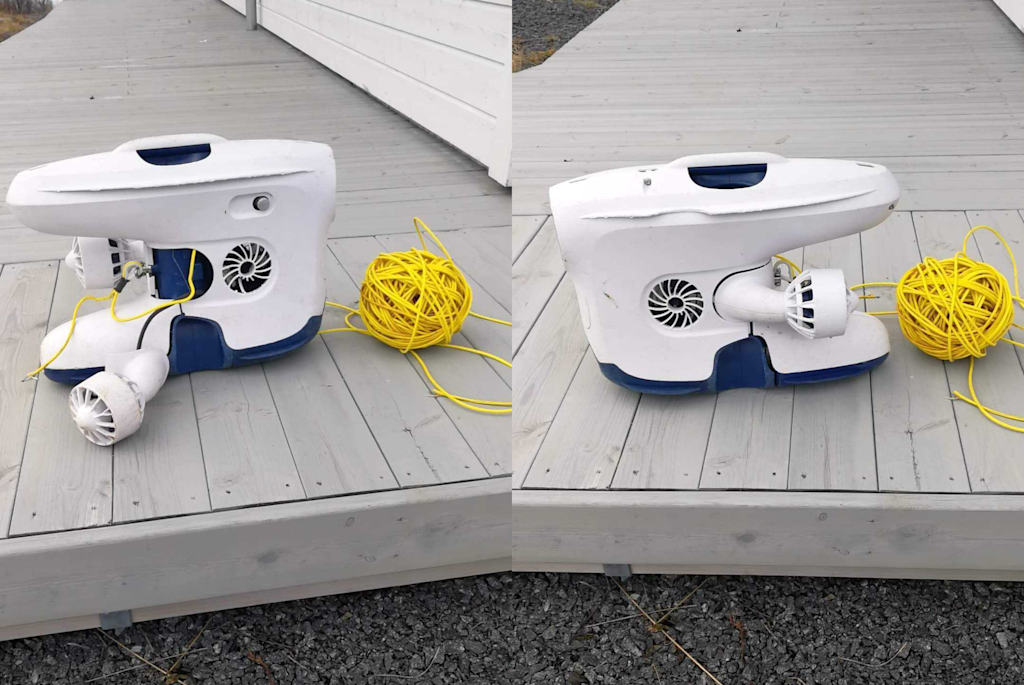
When we received the ROV for service in the Blueye office, it had some external damage to the thrusters and tether. Still, the rest of the drone barely had a scratch, and the inside was completely intact. We were able to fix their drone and send it back to them within two days. Since the ROVs inside were unharmed, they could retrieve all the video and images from their last operation. That's what we call a robust ROV!
We all claim that it's "user-friendly"
"User-friendly" has become cliché but inevitable when describing great products. We all demand that the products we use are easy to handle – why shouldn't we? Let us explain why the Blueye ROVs are indeed user-friendly.
Up and running in less than 1 minute
We dare to say that you'll be operational with the ROV in less than a minute. All you have to do on-site is to press a button to turn on the Surface unit, use the included magnet to turn on the ROV, launch the Blueye app on your phone or tablet, and connect to your chosen controller and the correct WiFi network. As simple as that.
Plug and play external equipment using Blueye Smart Connectors
The Blueye X3 ROV uses the Blueye Smart Connector to connect to external equipment. These smart connectors include a circuit board containing metadata about the connected equipment. If you connect a sonar, the Blunux operating system will start the necessary software modules automatically and seamlessly tell the Blueye App that a sonar is attached. There is no need for manual configuration, just plug it in and secure the equipment by fastening a screw or two.

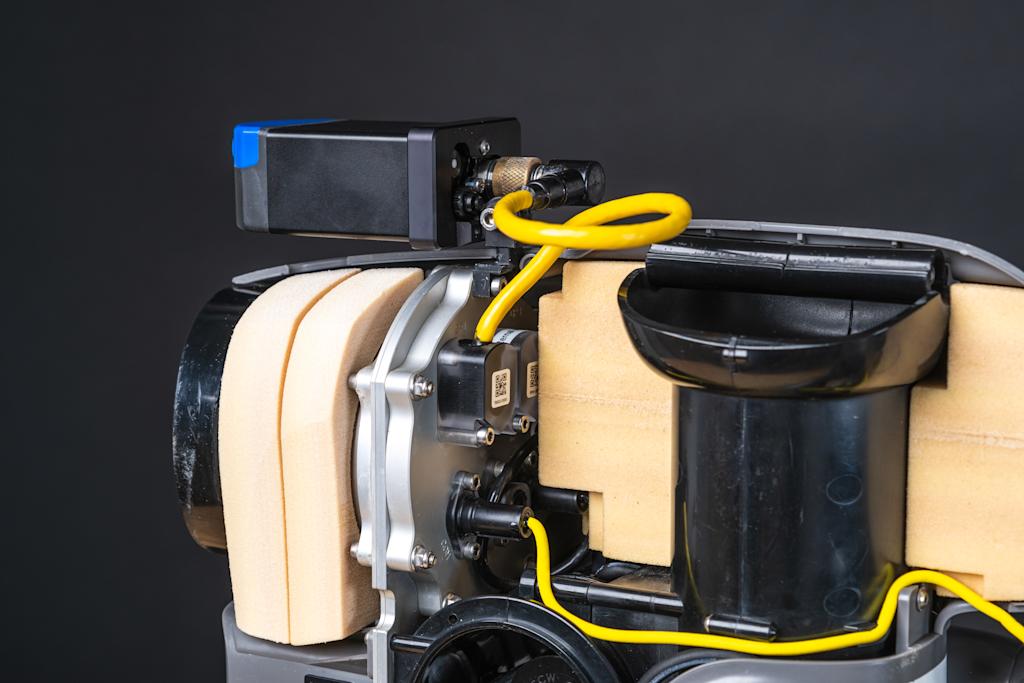
Maintenance and support are made simple with step-by-step instructions
Unless you are a real tech geek, you don't want to spend time debugging or configuring the vehicle; you just want it to function for the job in front of you. As a Blueye user, you'll have access to an extensive library of videos, manuals, articles, and other support functions in our Blueye Help Center. If you have a problem you can't seem to figure out yourself, our engineers are available for remote support.
The Blueye ROVs are also easily serviceable. All parts prone to wear are self-serviceable, and you can repair or replace them using basic tools.
Norwegian quality – all the way through
Blueye underwater drones are designed, developed, tested, manufactured, and supported in Norway.
As a leading ocean nation with one of the longest coastlines in the world, we take great pride in our knowledge of the sea. The Blueye team is putting down daily hours to uphold this legacy and prove why people continue to put their trust in Norwegian design and quality.
This may seem like big words, but let us explain what we mean by saying "Norwegian quality."
Automated test stations ensure the required quality in every ROV
Our manufacturing partner, Inission, is only 1 hour from the Blueye HQ. Inission has, since 2021, assembled and ran the Blueye ROVs through automated test stations to ensure the ROVs hold the required quality. One of several important test stations is the pressure chamber. Every single Blueye ROV goes through automated pressure testing to ensure no O-rings are missing or damaged and that the unit is completely sealed.

If a problem is detected in the different test stations, the Blueye team also receives a live notification in our internal communication system. This way, we can reach out directly to Inission to assist in resolving the issue in real-time.
Traceability and identification of all parts of a Blueye product
Full traceability and identification on all parts enable us to track and detect quality issues. Every single product we produce has its unique identification. Every electronics board is assigned a unique identification number, either as a QR code printed on the board, as a serial number written into the flash memory, or both. Even our smallest products, such as the Blueye Smart Connector Blindplug, have their own unique serial number printed on the plug and in the memory on the circuit board.
Testing in real environments
We don't have any clients (as far as we know) that use the Blueye ROV solely for diving in a pool. So why should we do our tests in one? We know our clients are out in murky waters, strong currents, and diving among structures such as fish pens, pipelines, and ships. Our office is strategically located right next to the Trondheim fjord, for us to quickly get out in all kinds of weather to test equipment and innovations in real environments.
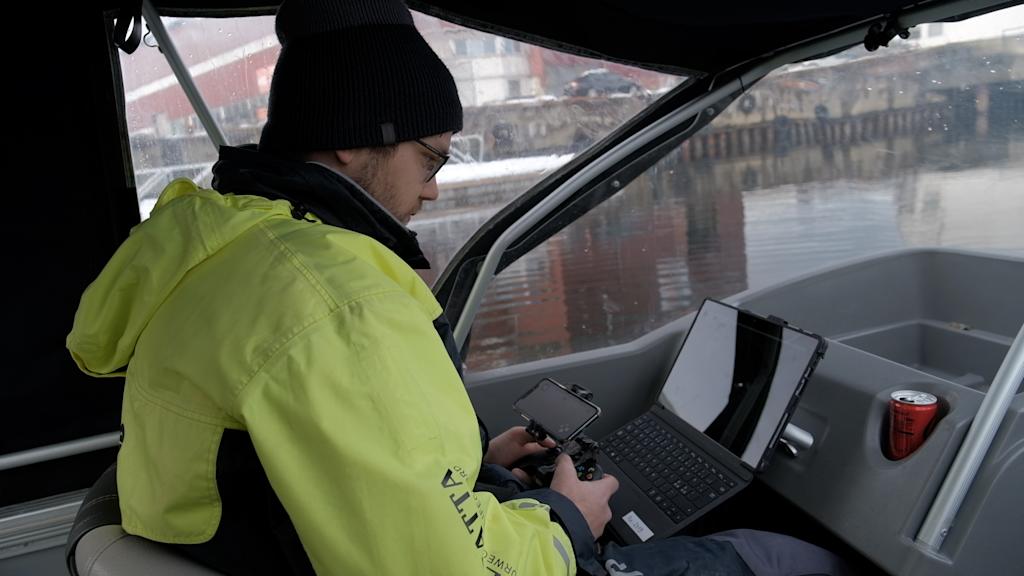
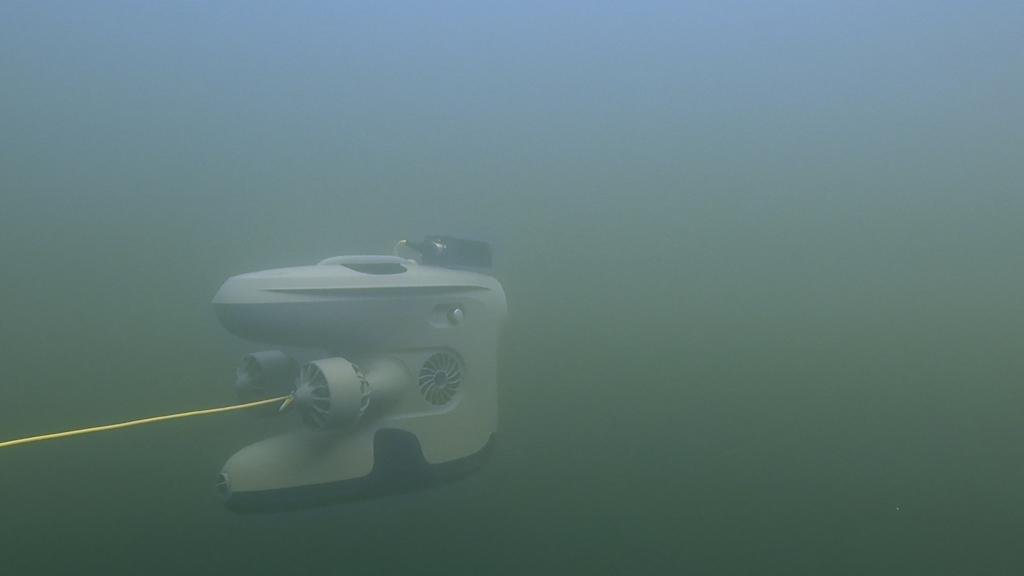
If you should ever need help with servicing your ROV
We talk about how easy it is to service the unit yourself. However, there are cases where you simply don't want to spend your time on this or special cases where more complicated errors occur.
We recently received a Pioneer ROV from 2019 with over 240 known dives in for a swift service. As you can see in the photo below, the ROV has been used extensively and the white cover has turned yellow. After a check, we suggested changing the thruster and the thruster cover and replacing the tether - making the yearly service cost, including new parts, down to only USD 450! That is low maintenance cost when the unit has been used at least 5 times per month on average.
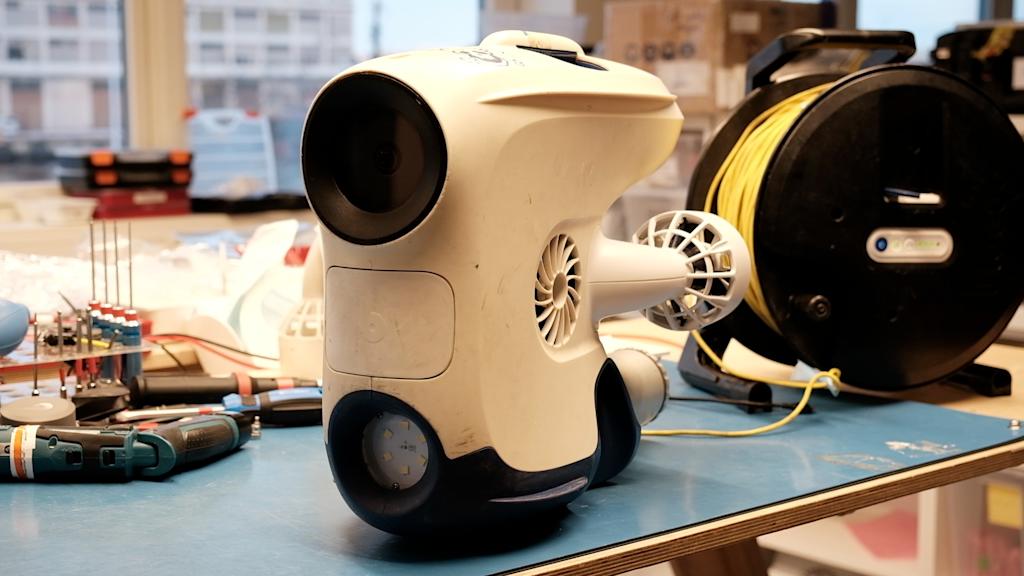